3D프린팅으로 10만 가지 부품 생산하는 '포드'
페이지 정보
작성자 최고관리자 작성일17-08-24 15:41 조회1,659회 댓글0건본문
불과 20년 전만 해도 3D 프린팅은 엔지니어의 장난감이었다. 하지만 지금은 3D 프린팅이 없으면 포드는 새로운 자동차를 만들어 내지 못할 것이다. 이 새로운 기술로 포드는 소비자와 가까운 곳에 생산설비를 가져올 수 있게 됐다.
Credit:IDG
현재 포드에서는 3D 프린팅 기술이 작동하지 않으면 사실상 자동차 개발이 중단된다.
20년 전, 자동차 산업에서 적층 가공은 소수 엔지니어가 시험 삼아 다루던 '틈새' 기술이었다. 그러다 10년 전 R&D 프로세스에 통합이 됐고, 지금은 개발 프로세스에 깊이 뿌리를 내렸다.
포드 제조부문의 고속 제조 기술 담당 기술 전문가인 해럴드 시어스는 "자동차 생산에서 3D 프린팅이 아주 큰 비중을 차지하고 있다. 도로부터 지붕까지 사실상 모든 프로토타입 제작에 3D 프린팅을 사용하고 있다"고 말했다.
3D 프린팅이 포드에 가져온 디지털 변혁은 어느 정도일까? 10여 년 전, 포드가 3D 프린팅을 이용해 제작한 자동차 프로토타입은 약 4,000종이었다. 지금은 5곳의 3D 프로토타이핑 센터에서 매년 10만 종 이상의 부품 프로토타입을 생산한다. 미래에는 프로토타입이 아닌 실제 자동차 부품 생산에도 적층 가공(3D 프린팅)을 사용할 전망이다.
더 많은 기업이 3D 프린팅 수용
프라이스워터하우스쿠퍼스(PwC)가 2016년 100대 제조사를 조사한 결과에 따르면, 고속 프로토타입 제작, 생산용(실제) 부품, 맞춤형 부품에 3D 프린팅을 사용하고 있으며 이 비율은 70%였다.
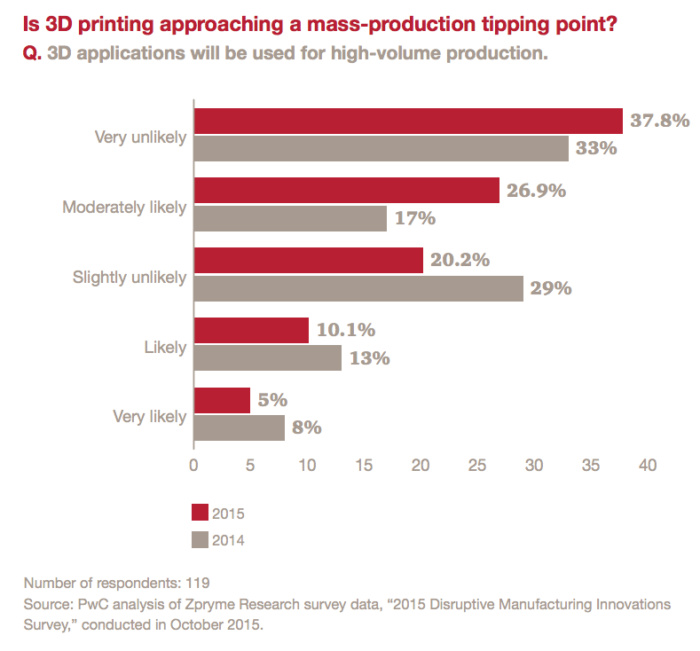
Credit:PWC
52%의 제조사는 3~5년 이내에 대량 생산 분야에서 2년 전보다 더 많이 3D 프린팅을 사용할 것으로 예상했다. 2년 전 이같이 예상한 제조사는 38%에 그쳤다. 또 67%는 5년 이내에 소량 전용 제품 생산에 3D 프린팅이 사용될 것으로 내다봤다.
IDC에 따르면, 2015년을 기준으로 했을 때 전세계 3D 프린팅 투자 규모가 110억 달러였으며, 2019년에는 270억 달러로 증가할 전망이다.
IDTechEx가 발표한 최신 보고서에 따르면, 3D 프린팅 금속 시장만 하더라도 2028년까지 120억 달러 시장으로 성장할 것으로 예상된다.
현재 프린터 기술 중 가장 지배적인 기술은 DMLS(Direct Metal Laser Sintering)이다. 지난해 말을 기준으로 했을 때 전체 설치 기반의 84%를 차지하고 있다. 나머지 3가지 주요 기술은 EBM(Electron Beam Melting), DED(Directed Energy Deposition), BJ(Binder Jetting)이다.
포드는 더 유용한 프로토타입을 만들고, 프로토타입을 넘어서는 틈새 애플리케이션(응용 분야)을 구현하기 위해 3D 프린팅에 금속 소재 사용을 늘렸다.
우주항공과 자동차 산업 등을 중심으로 적층 가공 기법이 생산 공정 일부로 정착됐다. 개발을 간소화할 수 있고, 부품 품질을 개선할 수 있고, 시간과 비용을 크게 절약할 수 있기 때문이다.
프로토타입을 이용한 시간 절약
포드 적층 가공 연구 부문의 기술 리더인 엘렌 리는 "부품 프로토타입 제작을 예로 들면, 3D 프린팅을 이용했을 때 아주 많은 시간을 절약할 수 있다. 도구를 만든 후 프로토타입 부품을 제작하는 방식에 걸리는 시간의 1/10밖에 되지 않는다"고 설명했다.
3D 프린팅을 이용, 기존 방식으로는 몇 주가 소요되는 프로토타입 부품을 며칠 만에 제작할 수 있다. 시어스는 "몇 달을 몇 주로 줄일 수 있다"고 말했다.
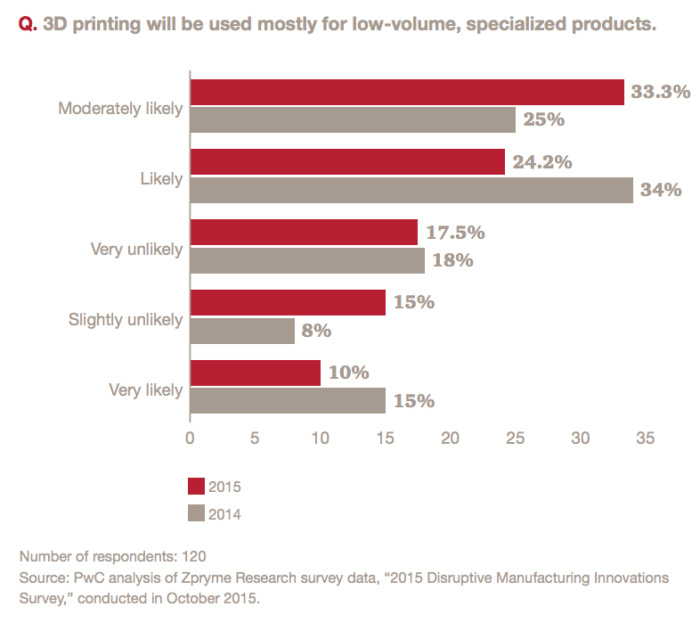
Credit:PWC
포드 엔지니어들이 3D 프린팅을 이용해 부품 개발 시간을 개선하기 위해 적용한 방법의 하나는 한 번에 각각 고유한 특징이 있는 여러 프로토타입을 제작하는 것이다.
과거 엔지니어들은 CNC 라싱 기계를 이용해 한 번에 한 개의 부품만 제작할 수 있었다. 또 프로토타입 부품 제작을 다른 회사에 위탁하는 회사들이 많았다.
시어스는 "과거에는 부품을 디자인하고, 도구를 제작한 후 부품을 만들어 테스트했다. 여기에서 끝나는 것이 아니다. 테스트 결과에 따라 도구를 수정해 또 다른 부품을 만들어 테스트해야 하는 경우도 있었다. 지금은 많은 엔지니어가 동시에 5~7개 부품을 제작해 넘겨준다. 모든 것을 한 번에 제작하는 것이다"고 말했다.
동시에 여러 프로토타입 부품을 이용할 수 있기 때문에 비교 테스트도 가능하다. 각각을 평가하기 위해 몇 주를 낭비할 필요가 없다.
관련링크
-
http://www.ciokorea.com/news/35299 1946회 연결